Färskvaruhuset
Färskvaruhuset works actively to stay one step ahead in terms of both laws and regulations and to meet its own requirements for quality and profitability. With the help of Jeeves ERP they have created the system support required for a cohesive flow
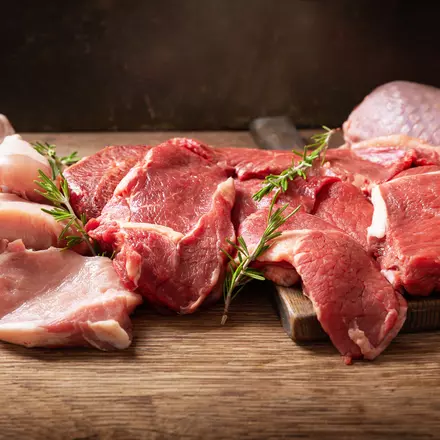
Optimizing the flow for goods and personnel
The food industry has strict rules regarding goods handling, and if the goods are perishables, the demands get even higher. That’s why Färskveruhuset turned to Jeeves ERP.
With strict rules regarding good handling of perishable goods causing increasing demands of its ERP system, Färskvaruhuset set out to address its challenges with modern, efficient IT support. Färskvaruhuset wanted to address these challenges using modern, efficient IT support. By giving staff the tools they need to work in a rational way, the company has managed to optimize the flow of goods in close collaboration with its Jeeves partner.
- At Färskvaruhuset, we work actively to constantly stay ahead of both laws and regulations and to meet our own standards of quality and profitability. By introducing Jeeves and an inventory management system developed by our partner, we’ve now have created the system support necessary for our employees to work in a cohesive flow, said John Dunklint, Project Manager at Färskvaruhuset.
From pen and paper to fully digital
As part of implemenenting Jeeves ERP, Färskvaruhuset has gone from pen, paper and handwritten pick lists to order placement online and order picking using a ring scanner and truck computer.
– Today, we’re increasingly using Jeeves as a platform for our daily operations, not only for order processing and inventory functions, but also for non-conformity management and complaints, which we’ve created our own functions for within the system, continued Dunklint.
Dealing with delicate foodstuffs demands traceability and temperature control. When goods are inspected upon arrival, the temperature and ‘batch ID’ are stored directly in the company’s database. With these tools, Färskvaruhuset can follow the product all the way from producer to consumer.
The process of introducing Färskvaruhuset’s new IT support has been a journey with many interesting challenges.
– Thanks to the close cooperation directly with our partner’s developers, we’ve identified the solutions that match our particular needs. Since we’re dealing with producers worldwide, we have, for example, had to take into account the Italian standard for EAN codes, which is quite different from our Swedish standard. The flexibility of Jeeves ERP also has helped us to maintain our broad range, but still have an efficient flow of goods and a smooth work process. We sell out our stock more than twice a week, so we demand a great deal from system support in terms of it being quick to work with at all levels, said Dunklint.
No picking errors and delivery notes always correct
– With the introduction of Jeeves ERP, we’ve consistently had better control of our stock availability, and by using the stock module, we now have 100 percent control. It also means that we basically have no picking errors, and information on delivery notes is always accurate. We also can now work with alternative sales units throughout the supply chain, that is, we can specify the same article in both kilos and boxes. We co-developed this function, as support for it was previously lacking. And, as a result of introducing the stock module, we’ve been able to maintain the same staffing levels as before, despite doubling the warehouse space, said Dunklint.